Bitumen Deposits in Alberta
Alberta’s oil sands are an extremely important resource to Canada. To put it in perspective, Canada holds the third largest proven oil reserves in the world and 97% is oil sands. Oil sands account for the majority of Canada’s crude oil production, 63% in 2019. Oil sand demand and production is expected to rise in the future.
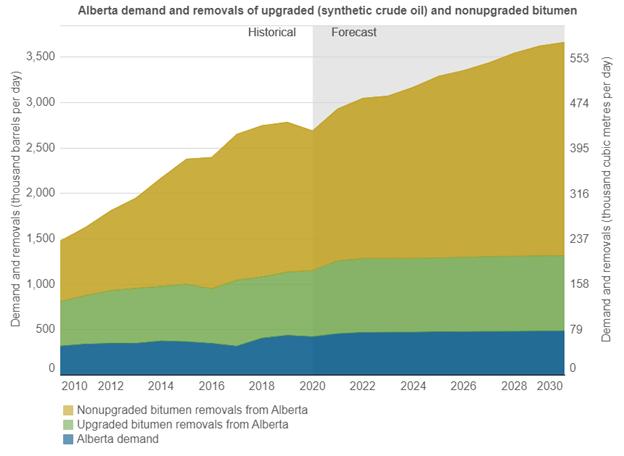
Oil Sands
Oil sands are sand and sandstone deposits soaked in bitumen. They consist of a mixture of sand, clay, water, and bitumen. Bitumen is extremely viscous heavy oil that does not flow easily on its own. This means conventional methods used to produce lighter crude oil do not work for oil sands, and alternate methods such as mining and thermal in-situ production must be used. Thermal in-situ production involves heating the bitumen up in the reservoir to reduce the viscosity, allowing it to flow up the wellbore and be produced. To transport bitumen, it is either heated or diluted with diluents (lighter hydrocarbons) to reduce its viscosity allowing it to flow.
Three primary regions, officially designated as “oil sands areas”, host bitumen deposits in Alberta. The largest by area and production is the Athabasca Oil Sands Area, spanning 93 000 km2. Bitumen is located primarily within the Wabiskaw Member and McMurray Formation sandstones. When people think of oil sands, they often think of open pit mining near Fort McMurray, however only 4 750 km2 (2% of the Athabasca Oil Sands Area) is surface minable area. The remainder of the bitumen in the Athabasca Oil Sands Area is produced using thermal production techniques to bring the bitumen to the surface. The other two oil sands areas in Alberta are the Peace River Oil Sands Area (over 29 000 km2) and the Cold Lake Oil Sands Area (nearly 18 000 km2).
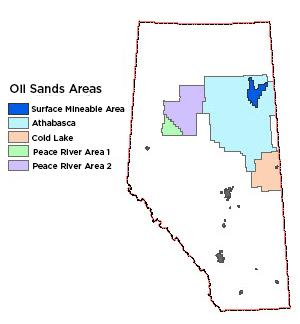
Oil sands close to the surface (less than 75 m underground) are extracted in open pit mining operations. Shovels scoop the oil sands into haul trucks and transport them to crushers where they are broken down and then mixed with hot water to be pumped to an upgrader. Upgraders convert bitumen to synthetic crude by reducing its viscosity and removing heavy fractions, sulphur, and metals, so it can be used by refineries. For areas deeper than this, the clearing of soil and rock above the oil sands (overburden) becomes too costly therefore the bitumen extraction requires underground in-situ methods using steam or steam with solvents.
Steam-Assisted Gravity Drainage (SAGD)
Steam-assisted gravity drainage, or SAGD (pronounced sag-dee), is a process that uses steam to heat the reservoir to reduce the viscosity of the bitumen. This requires drilling at least two horizontal wells: an injector well on top and an underlying producer well generally located 5 m below the injector well. The upper well injects steam into the reservoir, creating a steam chamber and heating the bitumen up, reducing its viscosity and allowing it to flow.
With the help of gravity, the now mobile bitumen and condensed steam flow to the lower producer well where they are pumped to the surface for transport, separation, and partial upgrading. Laterally continuous, horizontal mud beds above and below the well pair act as barriers to the steam chamber, either slowing or completely stopping its growth. SAGD is not currently economically viable for reservoirs containing less than 7 m in net pay thickness.
*This information is modified from the Alberta Energy Regulator’s report ST98.
Cyclic-Steam Stimulation (CSS)
Cyclic-steam stimulation (CSS), also known as the “huff and puff” method, varies from SAGD in that it only uses one wellbore that both heats and produces the bitumen. The CSS well cycles between 3 stages: injection, soak, and oil production. Steam is injected into a well at high temperature for a period of weeks to months to heat the oil in the surrounding reservoir. The CSS process recovers approximately 20% of the original bitumen in-place (OBIP). In comparison, steam-assisted gravity drainage recovers over 50% of OBIP.
In Alberta, CSS is predominantly used in the Cold Lake Oil Sands Area where it is implemented as a vertical-well process. It could also be applied on wells with multilateral horizontal legs. This would consist of alternately injecting steam with producing heavy oil and steam condensate. CSS works best in thick pay zones (>10 m) with high porosity sands (porosities 30% or higher).
*This information is modified from the Alberta Energy Regulator’s report ST98.